Published – 11/14/2022
Author – Ara Parsekian, Ph.D
Download as a PDF
Published – 11/14/2022
Author – Ara Parsekian, Ph.D
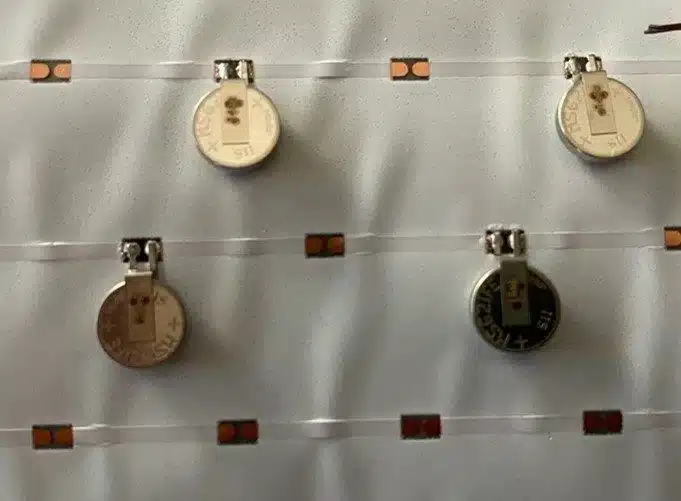
FIGURE 1: soldered battery test vehicle
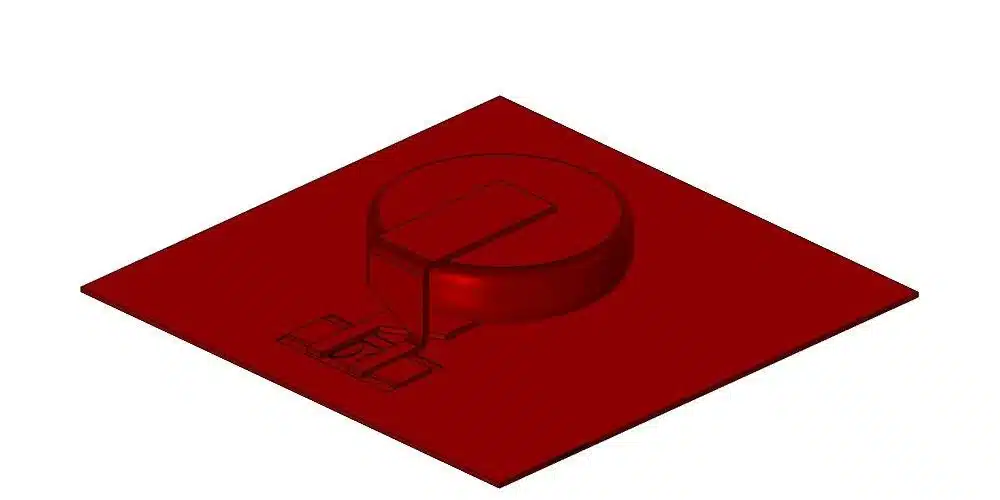
FIGURE 2: simulation of soldered battery
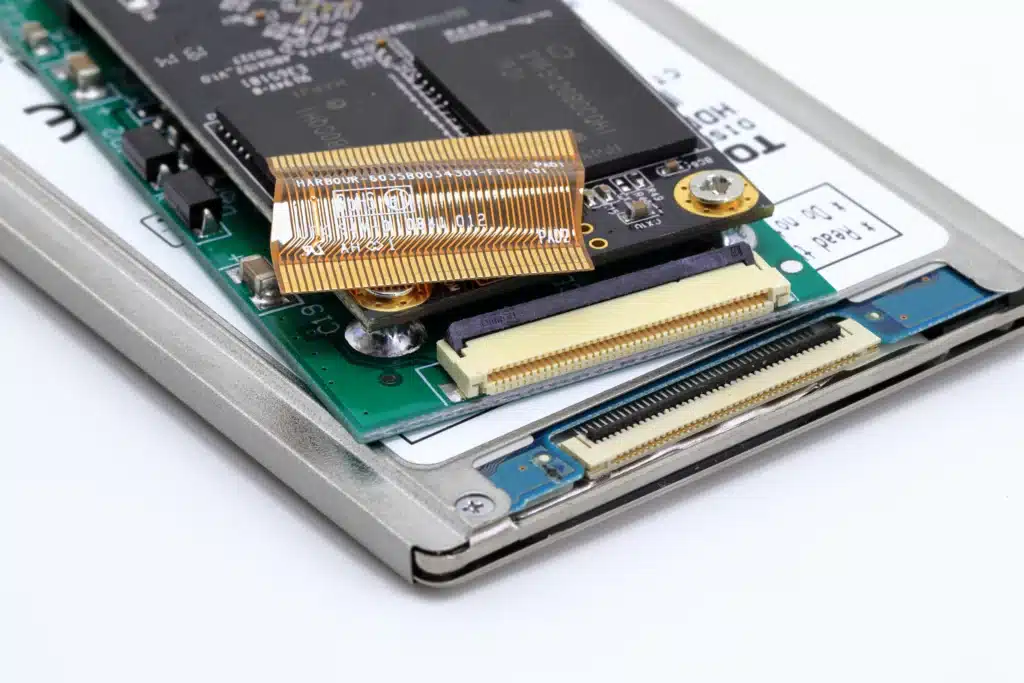
FIGURE 3: header for flex connector
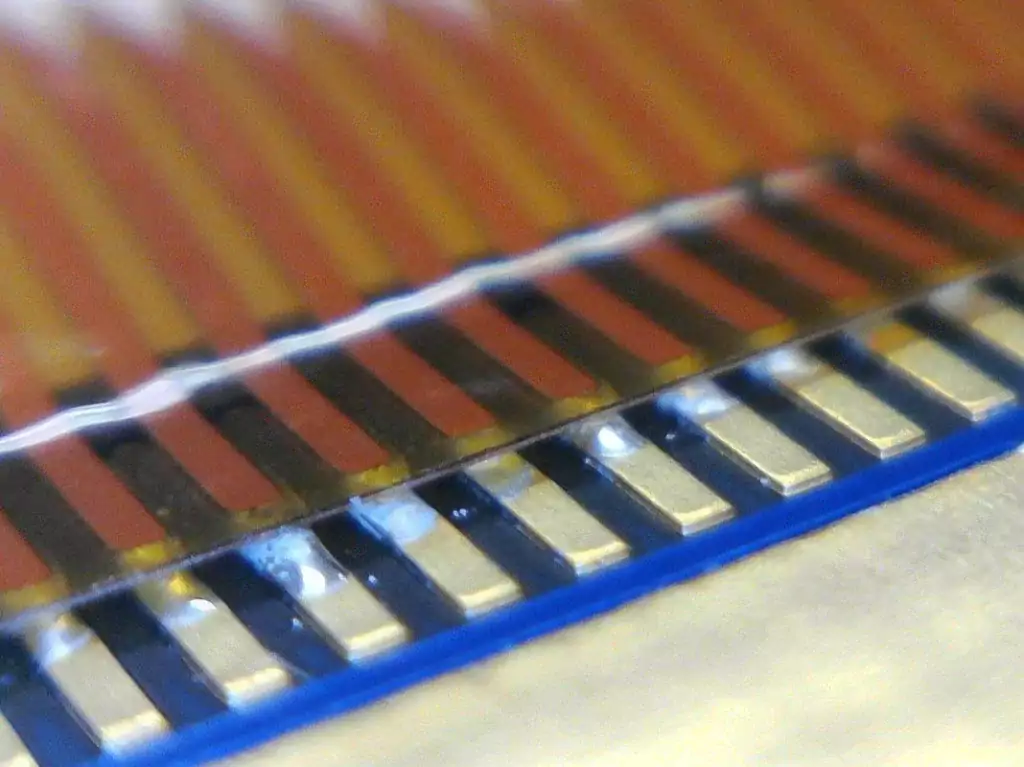
FIGURE 4: direct cable connection
In addition to these examples, the specifics of many a design project involve temperature limits that constrain how a PCB can be built. Of course, there are certainly workarounds that designers can use to get around the reflow step, or do away with solder altogether. But workarounds are taken out of necessity, and typically with some reluctance – they can increase unit costs, complicate supply chains, and sometimes, they can be the difference between a proof-of-concept and a viable commercial product. Photonic processing can be a powerful means to do away with the process workarounds and design the best product possible using materials that are not usable with legacy thermal processes.
*Please download PDF for references and citations.
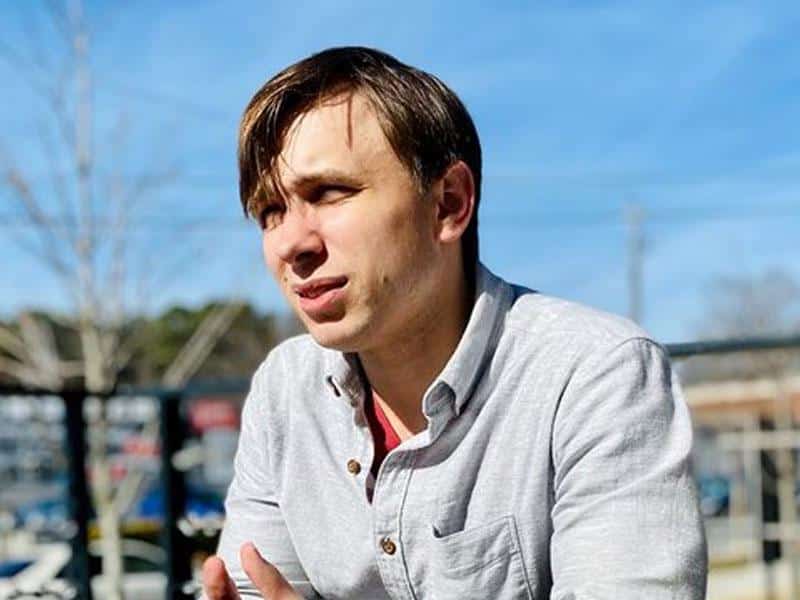
Ara Parsekian, Ph.D.
Applications Engineer,
PulseForge Inc
Related PulseForge in Research
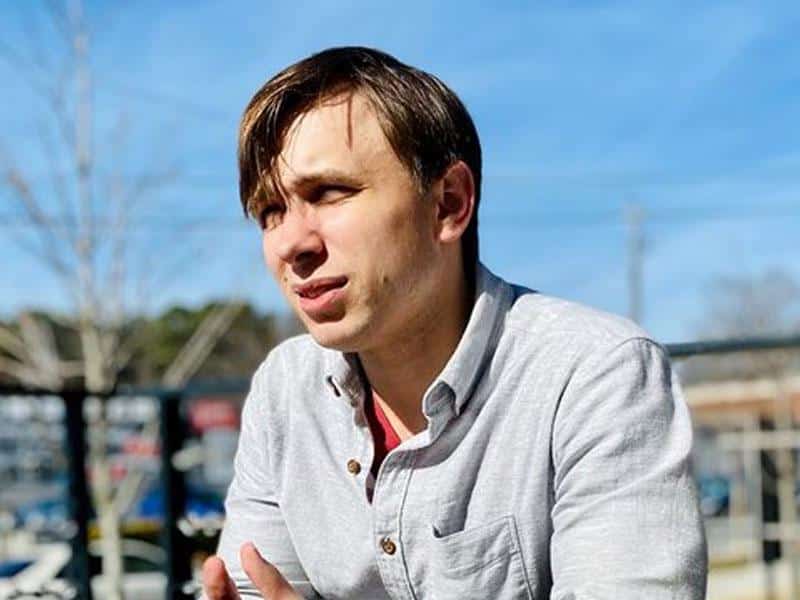
Ara Parsekian, Ph.D.
Applications Engineer,
PulseForge Inc