Processing Power for Research and University Labs
Highly configurable power in a compact package
A small footprint that was developed with options to meet your development needs
To make traces for the emerging printed electronics market, in 2005, our customers made dispersions of silver and copper nanoparticles, printing them on low-temp substrates, such as plastic and paper, and sintered them in ovens for 10-30 minutes. We discovered that we could get the same level of conductivity of printed traces with our newly developed flashlamp technology, and what took 10 minutes with ovens, was narrowed to 350 microseconds. We knew how many joules per cm2 the flashlamp put out – and we knew the absorptivity of the trace. A quick calculation revealed the peak temperature of the trace was hundreds of degrees C higher than the maximum working temperature of the substrate it was in direct contact with. Since thermal processes generally progress with the exponential of the temperature at which they are maintained, that explained why the curing was so fast – but with traces that hot, why was our technology not burning the substrates?
Because light is absorbed by traces, and not by substrates, and because our powerful light pulses are so short, traces are heated before they can equilibrate with the rest of the substrate. After exposure, which is of order 1 millisecond, traces thermally equilibrate with the bulk of the substrate after 10-50ms, depending on thickness. After a few 10s of milliseconds, the traces have been processed, the entire substrate and trace stack have equilibrated, and are only a few degrees warmer than they were after exposure, with no damage to the substrate.
Even plastics are not damaged because thermal damage, especially to polymers, takes a finite amount of time – our technology operates within that window, which is generally milliseconds. PET, as one example, has a maximum working temperature of about 150C, but PulseForge tools can briefly go up to about 400C. And with our extremely rapid flashlamp, and subsequent rapid cooling, thermal conduction is provided to the bulk of the substrate. We developed a regime allowing for high-temperature processing on low temperature materials without damage!
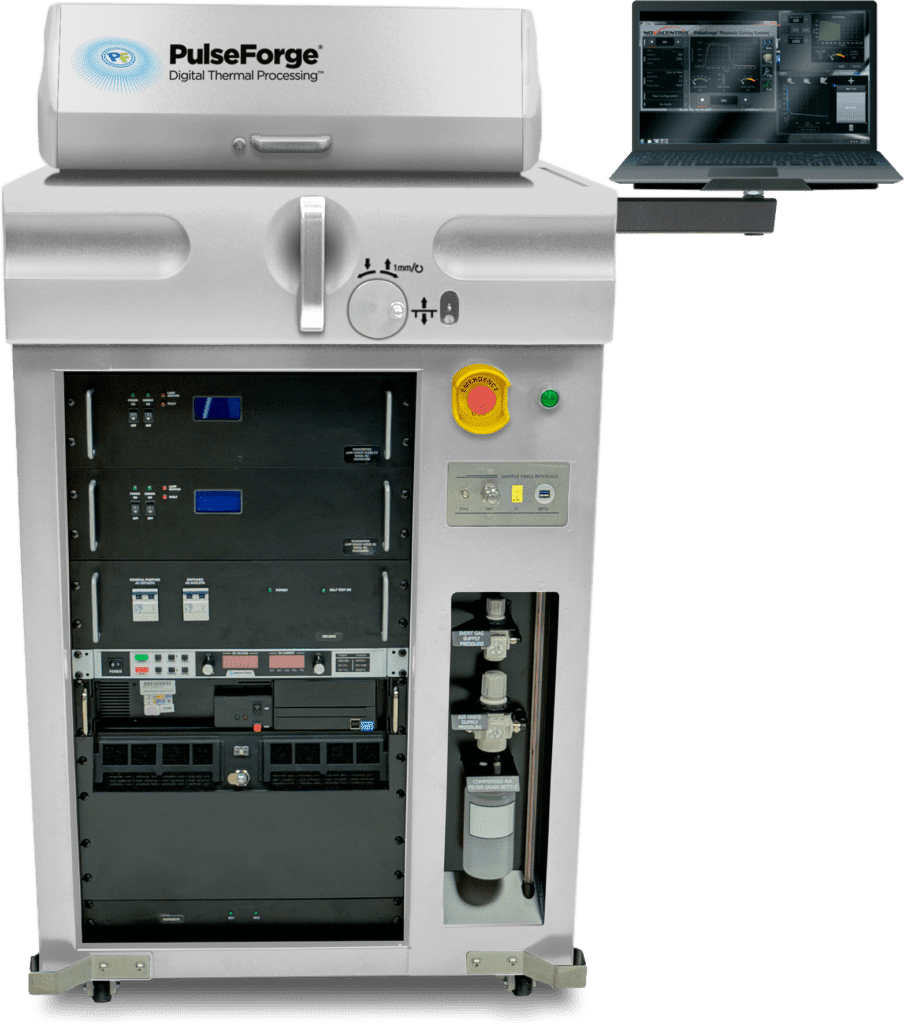
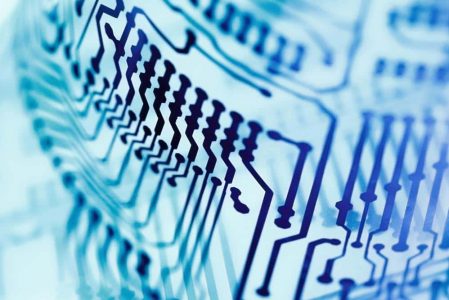
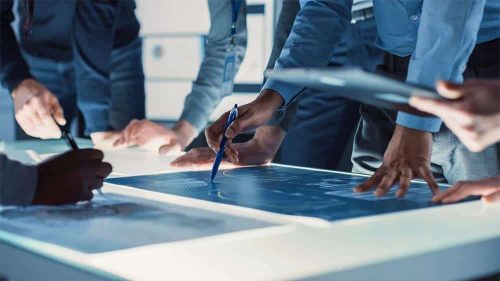
Highly configurable power in a small package
A small footprint that was developed with options to meet your development needs
To make traces for the emerging printed electronics market, in 2005, our customers made dispersions of silver and copper nanoparticles, printing them on low-temp substrates, such as plastic and paper, and sintered them in ovens for 10-30 minutes. We discovered that we could get the same level of conductivity of printed traces with our newly developed flashlamp technology, and what took 10 minutes with ovens, was narrowed to 350 microseconds. We knew how many joules per cm2 the flashlamp put out – and we knew the absorptivity of the trace. A quick calculation revealed the peak temperature of the trace was hundreds of degrees C higher than the maximum working temperature of the substrate it was in direct contact with. Since thermal processes generally progress with the exponential of the temperature at which they are maintained, that explained why the curing was so fast – but with traces that hot, why was our technology not burning the substrates?
Because light is absorbed by traces, and not by substrates, and because our powerful light pulses are so short, traces are heated before they can equilibrate with the rest of the substrate. After exposure, which is of order 1 millisecond, traces thermally equilibrate with the bulk of the substrate after 10-50ms, depending on thickness. After a few 10s of milliseconds, the traces have been processed, the entire substrate and trace stack have equilibrated, and are only a few degrees warmer than they were after exposure, with no damage to the substrate.
Even plastics are not damaged because thermal damage, especially to polymers, takes a finite amount of time – our technology operates within that window, which is generally milliseconds. PET, as one example, has a maximum working temperature of about 150C, but PulseForge tools can briefly go up to about 400C. And with our extremely rapid flashlamp, and subsequent rapid cooling, thermal conduction is provided to the bulk of the substrate. We developed a regime allowing for high-temperature processing on low temperature materials without damage!
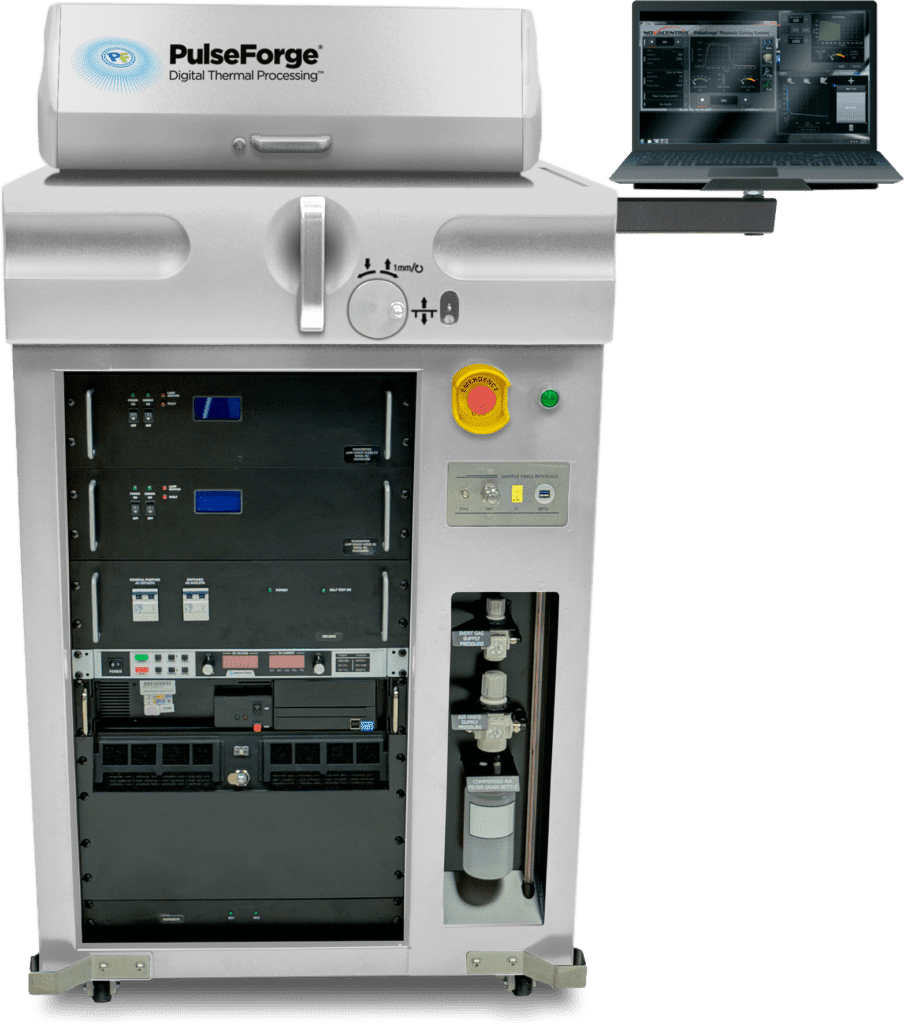
Discover Something Important
WE WANT TO UNDERSTAND YOUR RESEARCH NEEDS!
Curing
The Photonic Curing Revolution:
High-temperature processing on low-temperature materials
Sintering
Advanced Thermal Processing
Soldering
Soldering on temp-sensitive substrates (part 1)
Printing
Printing flexible patterns and traces
Debonding
Debonding in a fraction of the time, and ash-free
Soldering
Soldering on temp-sensitive components (part 2)
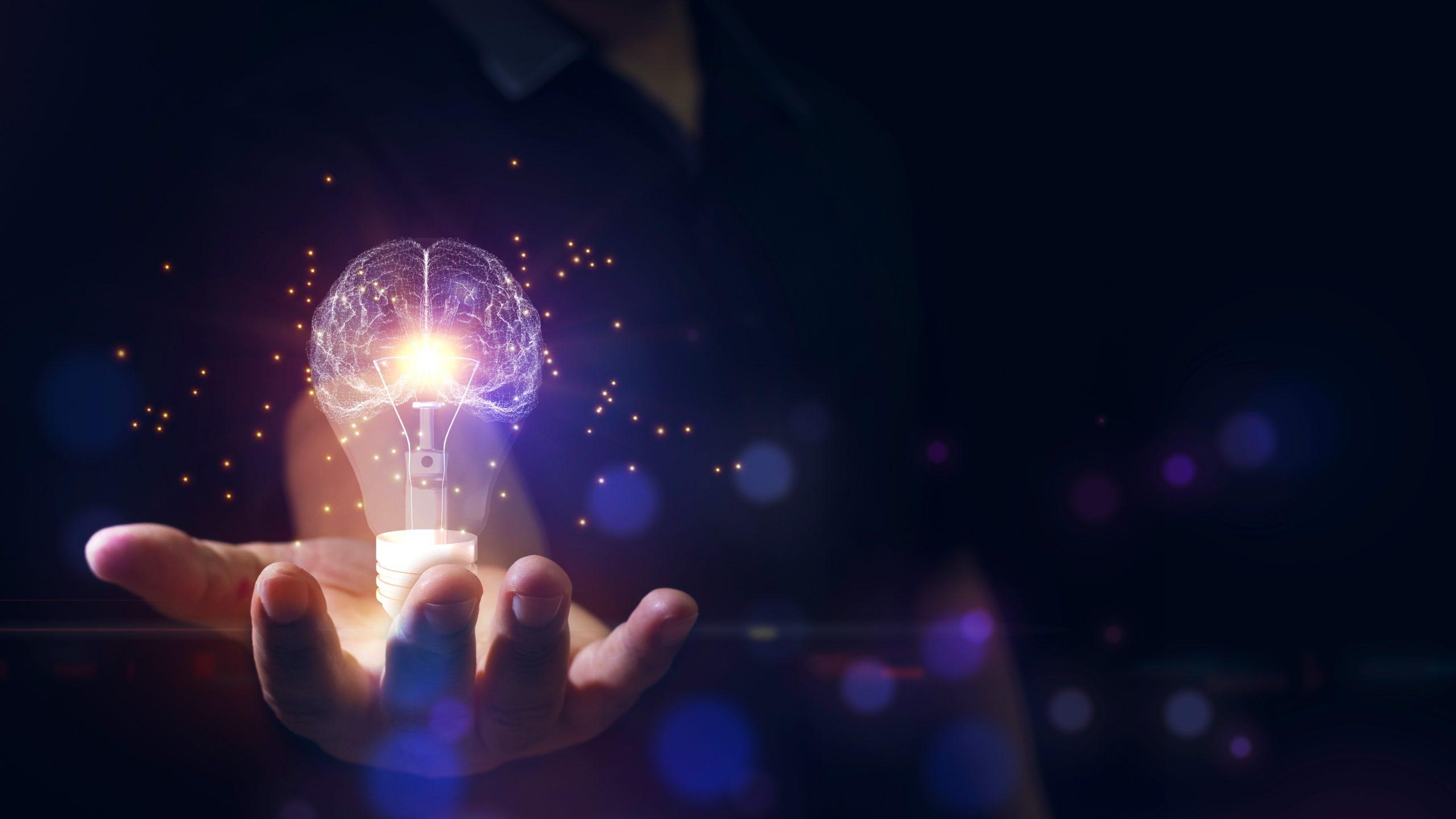
Rapid set-up + fast sample processing = more data in far less time!
- No damage to heat-sensitive, sustainable materials
- Milliseconds to seconds processing
- Small production and eco footprint
- Predictive tools processing with SimPulse for faster learning & iteration