Perovskites are a group of organometallic/all-inorganic halides with chemical formula ABX3 in perovskite crystal structure1. Considered as a next-generation photovoltaic (PV) material, they combine strong light absorption with superior carrier transport2 and tunable bandgaps3.
- Stability: perovskite degradation can be induced by humidity, heat and irradation7,8
- Scalability: large-scale defect-free thin film deposition is yet to achieve9These issues can be addressed by tailoring material properties, designing device structures as well as optimizing processing techniques. Photonic curing, as a power-intensive ultrafast photo-thermal technique, has the prospect for processing all the components in PSC.10–18
- For perovskite materials to achieve high temperature while circumventing thermal degradation
- For production to shorten processing time to less than millisecond scale combined with large-area capability
- For specific applications to comply with various flexible, temperature-sensitive substrates15
Photonic curing carried out by PulseForge tools is an ultrafast thermal process equipped with unrivaled exposure uniformity (Figure 1), fine-tuned power intensity and temporal profile modulation. Integration of perovskite deposition and in-situ photonic curing allows efficient and controllable removal of solvents from perovskite layers.
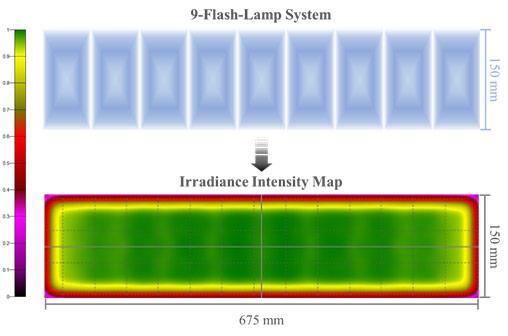
Troughton et. al. directly applied photonic-cured perovskite layer in mesoporous PSC under ambient conditions11. The resulting power-conversion efficiency was comparable to that obtained with conventional hot-plate annealing. The two-step hot-plate annealing included 90-min heating at 100 °C followed by another 10 min at 120° C conducted in a N2-filled glovebox, while the photonic curing process was done within a few milliseconds. In addition, the compatibility of photonic curing with ambient conditions alleviates significant practical barriers for industrial production in contrast to inert atmosphere annealing.
TiO2 annealed at 500° C for 30 minutes in a furnace was compared with photonically cured samples with a pulse duration of 7 ms on glass substrate (2 ms for the PET substrate) by Das et al17. Comparable performance was shown (15.0% and 11.2% on glass and PET, respectively), but photonic curing enabled millisecond processing time and a significantly lower thermal input compared with furnace heating.
![]() |
Written by Wen LiuAs an Application Engineering Intern this summer, Wen Liu has added great value to the team by utilizing her unique experience in solution-processible solar cells on flexible substrates, combined with the PulseForge® lift-off technique, towards fabrication of ultrathin and lightweight photovoltaics which are ideal for space and stratospheric applications. She is currently pursuing her Ph.D. at the Chemical Engineering department of University of Texas at Austin. Wen’s research focuses on nanocrystal synthesis and optoelectronic devices. Dedicating her academic pursuit to making efficient and flexible solar cells for ubiquitous applications, she steadily develops expertise in nanomaterial characterizations, thin-film deposition techniques as well as flexible electronics fabrication. Wen received her B.E. in Chemical and Biomolecular Engineering from Hong Kong University of Science and Technology, where she also worked as undergraduate research assistant on non-precious-metal-based electrocatalyst for hydrogen evolution reaction. |