Printing Flexible Electronics
Printing Flexible Patterns and Traces with Light
Published – 9/16/2022
Author – Harry Chou, Ph.D
In this ongoing series, we’ve talked about the transformational ability of digital thermal processing with PulseForge flashlamp systems to tune curing/converting processes for many types of materials. The impact of this ability on the field of printed flexible electronics has been shown with higher performance cured materials and tighter process control.
This degree of control has been extended to even show soldering processes using digital thermal processing with PulseForge tools. In last month’s article, we talked about reflowing lead-free solder alloys on low temp thermoplastic substrates in electronics assembly. Drawing a distinction between ‘heat’ and ‘temperature’ helped to illustrate how PulseForge is able to perform traditionally high temp processes on low temp substrates. The hot fudge sundae analogy was great for explanation and a great reminder to pick up some cool treats at the supermarket.
In this article, we’ll give a new example of how the level of control that is possible using PulseForge also enables other unique phenomena and other types of advanced processes.
From the device perspective, technology is moving toward adding more functionality to more materials, as well as lowering the cost and lowering the impact in materials themselves (and lowering the impact of the manufacturing processes).
From the process perspective, PulseForge process control has even more to offer. PulseForge has a solution in development for non-contact printing of different types of materials onto almost any surface. PulseForge can print ‘inks’ using a flash of light.
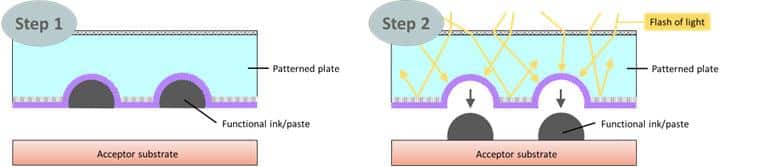
Figure 1. Illustration of the PulseForge Printing process with a functional ink/paste transferred from a patterned plate to an acceptor substrate by a flash of light.
PulseForge Printing is a process for patterning high aspect ratio prints of a wide variety of functional inks or other materials in a rapid, non-contact manner. The transfer of the ‘ink’ from the plate to the substrate in a ‘print’ is achieved with a high peak power pulsed light and a patterned print plate. The patterned wells in the plate, which contain the ‘ink,’ rapidly heat – causing volatile components to push it out from the plate and to the substrate. There are several facets of the printing process that are enhanced by the advanced capabilities of the PulseForge flashlamp. Tuning of the pulse condition, a capability that was described extensively in earlier articles, allows the user to create the proper high peak power pulse that will ‘print’ out their pattern and to make adjustments as-needed depending on their material, the pattern geometry, and the acceptor substrate. The uniformity of the PulseForge flashlamp output over a large exposure area is another critical capability which makes PulseForge Printing a compelling process. The relatively large window of the flashlamp (150 mm x 75 mm as standard) means that a large plate can be printed out at once, compared with a raster printing process.
A unique aspect of Printing with the PulseForge, because of the patterned print plate, is that the process is compatible with multi-thickness patterning. This can be considered a 2.5D printing technology. An example is a contact pad and lead frame pattern where the pads are pillars at a greater thickness than the leads (printed copper).
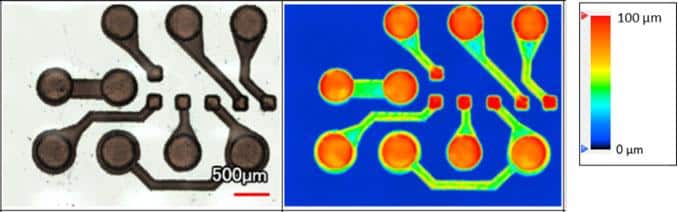
Figure 2. Printed copper ink showing different regions of the pattern having different height/thickness, representing a 2.5D printing capability when printing flexible electronics
Compared with other non-contact printing techniques, particularly inkjet and aerosol jet printing, PulseForge Printing is well-suited for high viscosity formulations giving thick prints (and there are a range of materials that will volatilize, eject, and print from patterned plates, given PulseForge’s control over pulse conditions). We have developed several high viscosity (> 1 M cps) copper and silver inks internally. We have also shown that many off-the-shelf lead-free solder pastes, SAC alloys as well as low-temperature Bi-containing alloys, can be printed using PulseForge.
As a non-contact printing technique, PulseForge Printing is compatible with almost any substrate. The main parameter to consider is adhesion between the ink and the substrate. The plate is designed such that the substrate is not exposed to the light pulse, which prevents damage to sensitive materials or components. The user can also print on non-flat surfaces and even over gaps. We have also demonstrated the ability to print and ‘swing-around’ an edge with silver conductive ink.
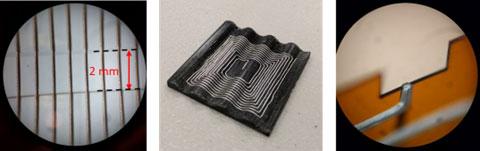
The capabilities of PulseForge Printing can add function and value to a wide range of device manufacturing processes. Some examples of this include: multi-thickness patterns produced in a single print can reduce process steps; conductive trace(s) bridging a gap or connecting across a panel can reduce process complexity; and the non-contact nature of PulseForge Printing enables additional functionality on more types of surfaces.
A few of these capabilities are particularly suited for achieving some of the goals in the fields of in-mold electronics and functional 3D printing. These two fields are working toward goals of adding more functionality to more materials through different approaches. The in-mold electronics approach adapts electronics and microelectronics fabrication processes to new materials, such as thermoplastic substrates, to create new functional devices. The adapted processes overlap significantly with many printed and flexible hybrid electronics processes, so printing and curing conductive inks is a critical capability for in-mold electronics. The functional 3D printing approach takes materials that have been used in devices and adapts them for 3D printing, like printing both a conductor and an insulator from a nozzle, for example. PulseForge tools provide unique processing and capabilities, while making formerly impossible to reach goals obtainable, and adding much needed functionality to everyday objects and environments.
*Please download PDF for references and citations.
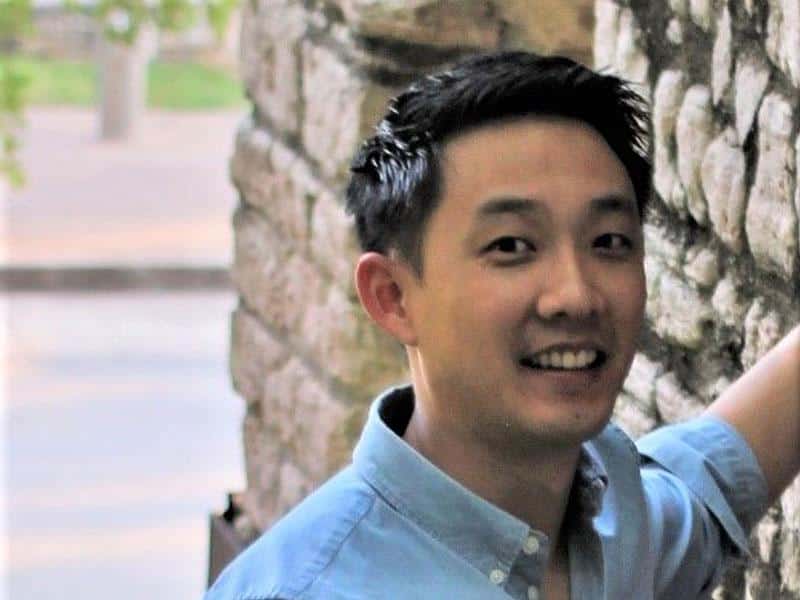
Harry Chou, Ph.D.
Applications Engineer,
PulseForge Inc
Related PulseForge Patent
Published – 8/16/2022
Author – Ara Parsekian, Ph.D
Download as a PDF
In this ongoing series, we’ve talked about the transformational ability of digital thermal processing with PulseForge flashlamp systems to tune curing/converting processes for many types of materials. The impact of this ability on the field of printed electronics has been shown with higher performance cured materials and tighter process control.
This degree of control has been extended to even show soldering processes using digital thermal processing with PulseForge tools. In last month’s article, we talked about reflowing lead-free solder alloys on low temp thermoplastic substrates in electronics assembly. Drawing a distinction between ‘heat’ and ‘temperature’ helped to illustrate how PulseForge is able to perform traditionally high temp processes on low temp substrates. The hot fudge sundae analogy was great for explanation and a great reminder to pick up some cool treats at the supermarket.
In this article, we’ll give a new example of how the level of control that is possible using PulseForge also enables other unique phenomena and other types of advanced processes.
From the device perspective, technology is moving toward adding more functionality to more materials, as well as lowering the cost and lowering the impact in materials themselves (and lowering the impact of the manufacturing processes).
From the process perspective, PulseForge process control has even more to offer. PulseForge has a solution in development for non-contact printing of different types of materials onto almost any surface. PulseForge can print ‘inks’ using a flash of light.
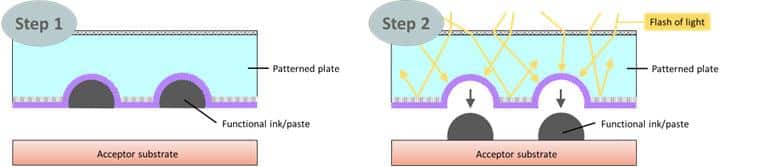
Figure 1. Illustration of the PulseForge Printing process with a functional ink/paste transferred from a patterned plate to an acceptor substrate by a flash of light.
PulseForge Printing is a process for patterning high aspect ratio prints of a wide variety of functional inks or other materials in a rapid, non-contact manner. The transfer of the ‘ink’ from the plate to the substrate in a ‘print’ is achieved with a high peak power pulsed light and a patterned print plate. The patterned wells in the plate, which contain the ‘ink,’ rapidly heat – causing volatile components to push it out from the plate and to the substrate. There are several facets of the printing process that are enhanced by the advanced capabilities of the PulseForge flashlamp. Tuning of the pulse condition, a capability that was described extensively in earlier articles, allows the user to create the proper high peak power pulse that will ‘print’ out their pattern and to make adjustments as-needed depending on their material, the pattern geometry, and the acceptor substrate. The uniformity of the PulseForge flashlamp output over a large exposure area is another critical capability which makes PulseForge Printing a compelling process. The relatively large window of the flashlamp (150 mm x 75 mm as standard) means that a large plate can be printed out at once, compared with a raster printing process.
A unique aspect of Printing with the PulseForge, because of the patterned print plate, is that the process is compatible with multi-thickness patterning. This can be considered a 2.5D printing technology. An example is a contact pad and lead frame pattern where the pads are pillars at a greater thickness than the leads (printed copper).
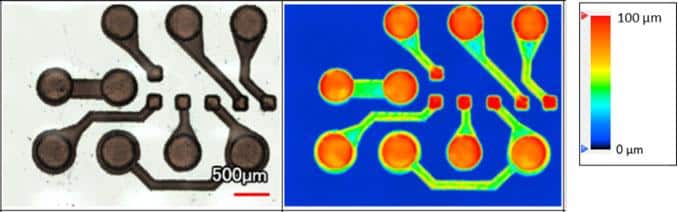
Compared with other non-contact printing techniques, particularly inkjet and aerosol jet printing, PulseForge Printing is well-suited for high viscosity formulations giving thick prints (and there are a range of materials that will volatilize, eject, and print from patterned plates, given PulseForge’s control over pulse conditions). We have developed several high viscosity (> 1 M cps) copper and silver inks internally. We have also shown that many off-the-shelf lead-free solder pastes, SAC alloys as well as low-temperature Bi-containing alloys, can be printed using PulseForge.
As a non-contact printing technique, PulseForge Printing is compatible with almost any substrate. The main parameter to consider is adhesion between the ink and the substrate. The plate is designed such that the substrate is not exposed to the light pulse, which prevents damage to sensitive materials or components. The user can also print on non-flat surfaces and even over gaps. We have also demonstrated the ability to print and ‘swing-around’ an edge with silver conductive ink.
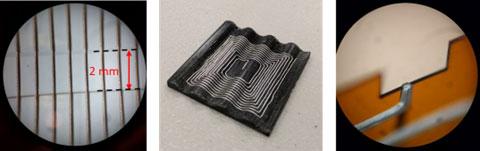
The capabilities of PulseForge Printing can add function and value to a wide range of device manufacturing processes. Some examples of this include: multi-thickness patterns produced in a single print can reduce process steps; conductive trace(s) bridging a gap or connecting across a panel can reduce process complexity; and the non-contact nature of PulseForge Printing enables additional functionality on more types of surfaces.
A few of these capabilities are particularly suited for achieving some of the goals in the fields of in-mold electronics and functional 3D printing. These two fields are working toward goals of adding more functionality to more materials through different approaches. The in-mold electronics approach adapts electronics and microelectronics fabrication processes to new materials, such as thermoplastic substrates, to create new functional devices. The adapted processes overlap significantly with many printed and flexible hybrid electronics processes, so printing and curing conductive inks is a critical capability for in-mold electronics. The functional 3D printing approach takes materials that have been used in devices and adapts them for 3D printing, like printing both a conductor and an insulator from a nozzle, for example. PulseForge tools provide unique processing and capabilities, while making formerly impossible to reach goals obtainable, and adding much needed functionality to everyday objects and environments.
*Please download PDF for references and citations.
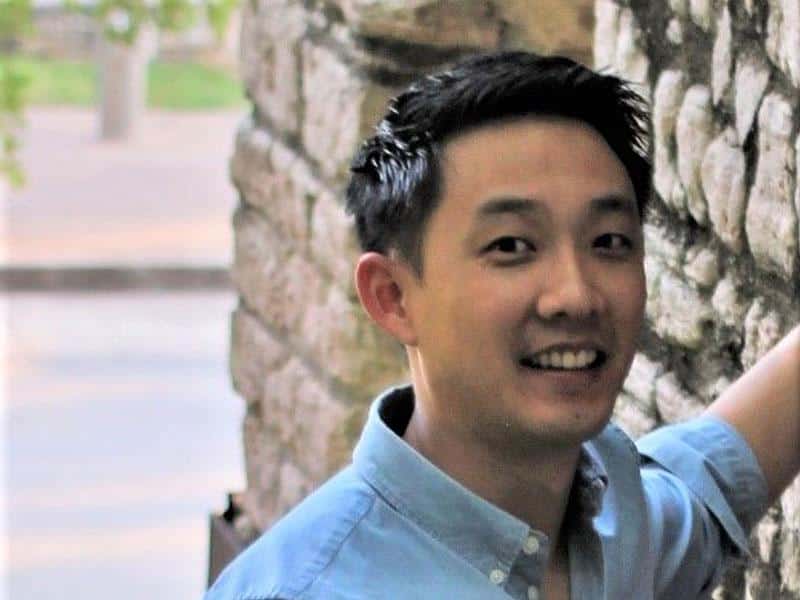
Harry Chou Ph.D.
Applications Engineer, PulseForge Inc