Choosing the appropriate technologies for your electronics assembly line is essential. And from board design to product reliability to production capacity, the reflow step is a critical part of that choice. In this blog, we’ll take a close look at one option with unique and powerful advantages: photonic soldering using Digital Thermal Processing™ from PulseForge®
Photonic soldering is a rapid and high-precision component attachment method, where heating is accomplished with high-intensity pulsed white light, quickly heating and melting the solder. It offers excellent solder joint quality, with high uniformity and consistency, exceptionally low void density, and low thermal impact on sensitive components.
Photonic soldering is especially useful for thermally-sensitive components and materials, because it selectively heats at the surface layer with low overall thermal energy. In fact, since photonic soldering is so rapid, thermal equilibrium is not reached until after the process has completed. In other words, the process of solder reflow occurs faster than the rate of heat conduction into thermally-sensitive parts of the PCB. This makes photonic reflow ideal for use on components such as batteries, and on flexible plastic substrates that can’t withstand heating in a convection oven.
Photonic soldering is highly energy efficient, using less than 15% of the energy consumed by a convection oven. The secret is low total energy delivered extremely quickly. Because photonic soldering works by delivering less overall heat, it’s an extremely energy-efficient process. And since the process can ramp up in seconds, no energy — or warmup time — is wasted when changing settings or turning on the tool. In addition, photonic soldering has a small footprint, with convection ovens taking up to six times the floor space of a photonic tool.
Although photonic soldering’s footprint is small, its throughput is high. Since all solder pads within the light exposure area are processed simultaneously, it can be hundreds or thousands of times faster than laser soldering for high-density PCB layouts. Compared to other soldering technologies, photonic soldering offers excellent cycle times. In addition, process settings can be adjusted with virtually no downtime, so process conditions can be adjusted on demand, with minimal line programming required.
Your company can access these advantages by adding PulseForge® In-Line series equipment to your assembly line. Your custom integration projects can be accommodated by the PulseForge® Embed series external power rack and embedded lamp assembly. Please do not hesitate to contact us at Pulse Forge, by email or phone call, to discuss your technical questions and production needs in greater depth. We will be delighted to interact with you. PulseForge, Inc.
PulseForge, Inc.
pf.sales@pulseforge.com
+1 (512) 491-9500
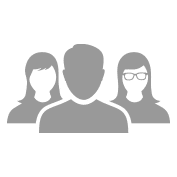
Written by the PulseForge Applications Team
Contact Us
Please contact us at PulseForge to discuss your technical questions and production needs — we look forward to hearing from you.
pf.sales@pulseforge.com
+1 (512) 491-9500