The digital nature of processing on PulseForge tools enables us to manufacture in a varying of form factors. A significant rethinking of how electronics are manufactured enables us to create a near-continuous production line in a roll-to-roll (R2R) format. In collaboration with the Holst Center – a leading innovation center in flexible and printed electronics –NovaCentrix has built a scalable PulseForge platform that allows reflow of standard lead-free solder on polymeric foils in a roll-to-roll format.
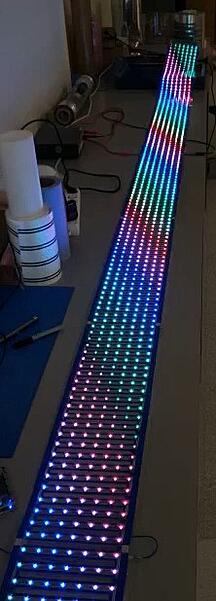
(above image: RGB LEDs on PEN produced on the pilot line)
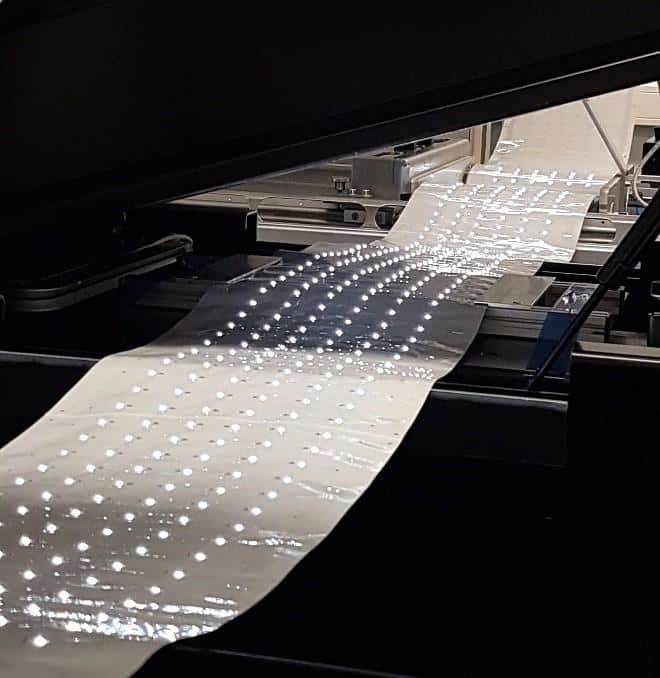
(above image: roll of 0603 LEDs on PET produced on the pilot line)
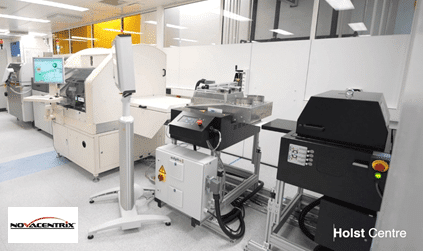
(above image: pilot line with integrated PulseForge at Holst Center, Netherlands)
- High throughput
- Low-cost operation
- Fully automatic
- Multiple sequential processing steps
- Handles varieties of substrates and components
- SMEMA compatible
- Light shielding
- Safety interlocks
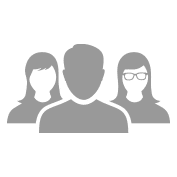
Written by the PulseForge Applications Team
Contact Us
Please contact us at PulseForge to discuss your technical questions and production needs — we look forward to hearing from you.
pf.sales@pulseforge.com
+1 (512) 491-9500